Getting Started
MemsFCR generates a CSV (comma separated values) file that can be used by this Online Analysis tool. Version 2.4.1 and higher creates an additional FCR file which is in JSON format. The CSV file if very useful for loading into Excel or similar, whereas the FCR file contains only the data required for analysis but also contains the ECU Id, Serial number and the ability to add some notes in a Summary field. Both files are supported in this online analyser, however in preference upload the FCR file.
Upload the MemsFCR Log File using the drop zone below. The file will be uploaded and processed and a diagnostic report provided outlining any detected faults.
Each parameter from the ECU is displayed in Tabular format and as Graphs.
If the CSV file is incompatible then the upload will be rejected. The online analyser will use the ECU raw data only.
If the Upload of a CSV file fails, then check that your logfile contains the following key columns:
'#time' this field contains the timestamp
'0x7d_raw' this field contains the ECU response to the command 0x7D
'0x80_raw' this field contains the ECU response to the command 0x80
MemsFCR Online Analysis
The Manifold Absolute Pressure Sensor (MAP) provides information about the pressure in the intake manifold. This information is used to calculate the air density and the air mass ratio. A leak in the vacuum pipes will adversely affect performance as the ECU will be unable to calculate the correct air to fuel ratio. Until the ECU has determined a fault condition this can result in very erratic engine behaviour.
The Coolant temperature sensor (CTS) measures the temperature of the water circulating the engine. The Mini SPi should be fitted with an 88C thermostat to ensure correct operating temperature is reached. Below 80C the ECU will determine that the engine is still warming and may over-fuel and remain in open loop where the Lambda (O2) readings are not used to adjust the air fuel ratio. This sensor is also used to determine if the electric fan should be activated and the engine temperature on the instrument panel.
The Air Temperature Sensor (ATS) also referred to as the Intake Air Temperature Sensor measures entering the air filter (where the sensor can be located). If the sensor is open circuit, then a fixed default value will be displayed. The inlet air temperature is used by the ECU to retard the ignition timing to avoid knock and trim the fuelling when hot. If the sensor is not operating correctly the engine performance may be impaired slightly.
The Lambda Sensor or oxygen sensor (O2) measures the amount of oxygen in the exhaust gases. If there is too much oxygen then the ECU will add more fuel to enrich the mixture. If there is too little oxygen in the exhaust then the ECU will reduce the fuel and decrease the making the mixture more lean. The ECU tries to balance the air : fuel ratio using the ECU mapping table. When operating in closed loop the ECU will use the dynamic values read from the O2 sensor and the engine RPM sensor to adjust the air : fuel ratio.
The Crankshaft Angle Sensor (CAS) also referred to as the Crankshaft Position Sensor, this sensor is used to 'synchronise' the engine at start-up, so that the ECU knows when to inject the fuel. The crankshaft position sensor is often used as a source to measure the engine speed. A fault with this sensor has a direct effect on the overall operation of the fuel injection system and will create very erratic behaviour including stalling and misfires.
The Throttle Position Sensor (TPS) is used to determine the position of the accelerator pedal. As the accelerator pedal is pressed the amount of air and fuel is increased. On the Mini Spi the TPS is used to determine the throttle position with reference to Idle Air Control (IAC) sensor.
The Idle Air Control Sensor (IAC / IACV) is used to adjust the engine idle speed when starting from cold. The ECU increments and decrements the Stepper Motor to adjust the throttle. The ECU has no direct feedback as to the position of the stepper motor. The ECU attempts to reset the stepper motor when the ignition is switched on by applying a voltage for a short period. The IAC position can give an indication of a faulty stepper motor.
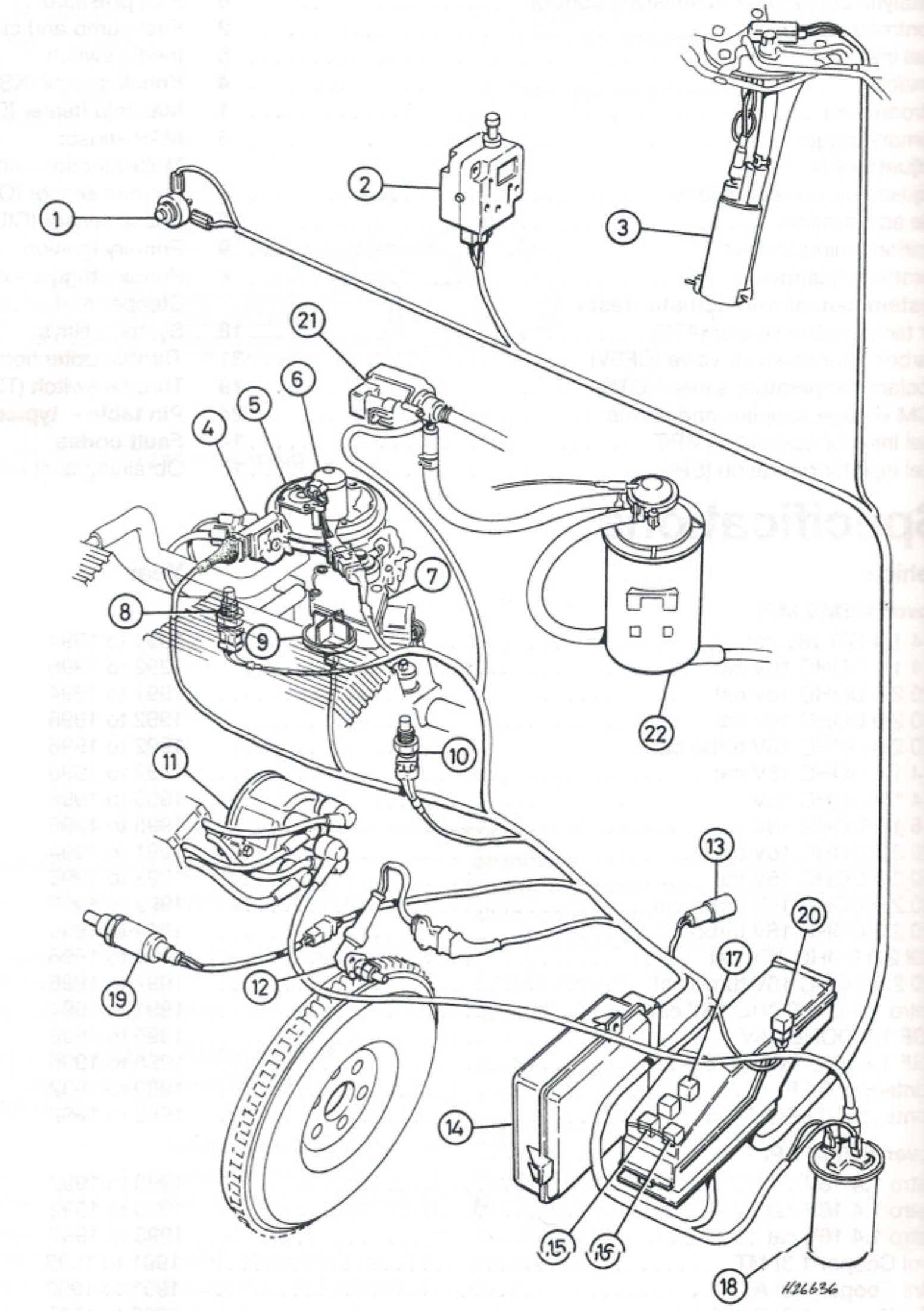
- Throttle pedal switch (pre-1993)
- Inertia Switch
- Fuel Pump
- Throttle pot. sensor (TPS)
- Fuel pressure regulator
- Fuel injector
- Stepper motor (IAC)
- Air (Intake) Temperature Sensor (ATS)
- Throttle body header (PTS)
- Coolant Temperature Sensor (CTS)
- Distributor
- Crankshaft Angle Sensor (CAS)
- Diagnostic connector
- MEMS ECU
- Main relay
- Fuel pump relay
- Throttle body heater relay
- Ignition coil
- Lambda (Oxygen) Sensor (OS)
- Lambda Sensor heater relay
- Carbon filter solenoid valve (CFSV)
- Charcoal canister
The main engine load sensor is the MAP sensor. A vacuum hose connects the MAP sensor (located within the ECU) and the inlet manifold.
Manifold vacuum acts upon the MAP sensor diaphragm, and the ECU converts the pressure into an electrical signal.
MAP is calculated from the formula: Atmospheric Pressure less Manifold Pressure = Manifold Absolute Pressure.
Using the speed/density method, the ECU calculates the AFR from the MAP signal and the speed of the engine (CAS).
This method relies on the theory that the engine will draw in a fixed volume of air per revolution.
The.inlet manifold on the MPi models is a 'dry' manifold. Since fuel does not enter the manifold - due to injection being made onto the back of the inlet valve,
there is no risk of fuel being drawn into the MAP sensor to contaminate the diaphragm, and a fuel trap is not used.
The inlet manifold on the SPi models is a 'wet' manifold. Fuel is injected into the inlet manifold, and there is a risk of fuel being drawn into the MAP sensor to contaminate the diaphragm.
This is prevented by running the vacuum hose upward to the air filter, through a fuel trap and then to the ECU (which contains the MAP sensor).
The CTS is incorporated in the cooling system, and contains a variable resistance that operates on the NTC principle.
When the engine is cold, the resistance is quite high. Once the engine is started and begins to warm-up, the coolant becomes hotter, and this causes a change in the CTS resistance.
As the CTS becomes hotter, the resistance of the CTS reduces (NTC principle), and this returns a variable voltage signal to the ECU based upon the coolant temperature.
The open-circuit supply to the sensor is at a 5v reference level, and this voltage reduces to a value that depends upon the CTS resistance.
Normal operating temperature is usually from 80°C to 100°C. The ECU uses the CTS signal as a main correction factor when calculating ignition timing and injection duration.
The coolant temp sensor is the black sensor located in the inlet manifold. It can be found underneath on the right side of the manifold as you stand at the front of the car.
The coolant temperature sensor works on the same principle as the air temperature sensor, whereby as the temperature falls the resistance rises or vica versa.
A faulty CTS will have a dramatic effect on the fuelling of the engine as the ECU may never leave the cold start and warm up programs which operate in
open loop control where the signal from the oxygen sensor is almost ignored.
Again this sensor will usually read out low and a permanently rich condition will result.
This sensor is connected directly to the ECU and then the ECU provides a signal to the Temperature Gauge on the dash.
The gauge should read not quite midway, just a little below the white line when the engine is warm.
It's always worthwhile checking the plug connectors as these can suffer contact corrosion.
This sensor can only be accurately checked with the diagnostic and a calibrated thermometer.
If this sensor is faulty and causes the ECU to over fuel for long periods, the Oxygen Sensor will usually fail too.
The ATS is mounted in the air inlet casing (MPi) or air filter casing (SPi), and measures the air temperature before it enters the inlet manifold.
Because the density of air varies in inverse proportion to the temperature, the ATS signal allows more accurate assessment of the volume of air entering the engine.
The open-circuit supply to the sensor is at a 5.0v reference level, and the earth path is through the sensor return.
The ATS operates on the NTC principle. A variable voltage signal is returned to the ECU based upon the air temperature.
This signal is approximately 2.0 to 3.0 volts at an ambient temperature of 20°C, and reduces to about 1.5v as the temperature rises to around 40°C.
Although the air filter casing used on SPi models contains a thermal valve system, the air temperature is calculated solely by reference to the ATS.
The air temperature sensor is the green plug and sensor mounted in the underside of either of the types of air filter, Standard or K&N.
This sensor is used by the ECU to determine the density of the air entering the engine. The sensor does not have to totally fail to cause issues with engine running.
The sensor is a NTC (Negative Temperature Coefficient) thermistor, resistance rises as the temperature falls.
The sensor element is constructed of two dissimilar metal wires fused together (the bead) at the tip of the sensor, this generates a resistance that changes with temperature.
This type of sensor is prone to contamination with moisture which causes corrosion at this fused point, generating a higher resistance.
It will most likely give a low reading compared to the actual air entering the engine and the ECU will determine the air is denser (colder) than it is and add more fuel to compensate.
The Rover part number is NNK10001
This only contributes to 20% of the fueling equation with the main reasons for rich running being the Throttle Position Sensor and the Coolant Temperature Sensor.
When this sensor fails, causing rich running conditions, it usually causes the Oxygen Sensor to fail as the carbon particles clog the pours of the sensor.
Symptoms of rich running are black sooty spark plugs( make sure the correct plugs are used first NGK BPR6ES), rich misfire, erratic idle and elevated CO and Hydrocarbon emissions.
The MEMS injection system fitted to catalyst vehicles implements a closed-loop control system, so that exhaust emissions may be reduced. Closed-loop systems are fitted with an oxygen sensor (OS) (Lambda Sensor) which monitors the exhaust gas for its oxygen content. A low oxygen level in the exhaust signifies a rich mixture. A high oxygen level in the exhaust signifies a weak mixture. The lambda voltage will be seen to oscillate between a high reading and a low reading in normal operation. The OS only produces a signal when the exhaust gas, has reached a minimum temperature of approximately 300°C. In order that the OS will reach optimum operating temperature as quickly as possible after the engine has started, the OS contains a heating element. The OS heater supply is made from the OS relay terminal number 87 (on the right hand side of the engine bay on an Spi). This ensures that the heater will only operate whilst the engine is running. Under full-load conditions, the heater supply is cut-off by the ECU by inhibiting the earth path of the OS relay.
The primary signal to initiate both ignition and fuelling emanates from a Crankshaft Angle Sensor (CAS), also referred to as the Crankshaft Position Sensor which is mounted next to the flywheel. The CAS consists of an inductive magnet that radiates a magnetic field. The flywheel incorporates a reluctor disk containing 34 steel pins set at 10° intervals. As the flywheel spins, and the pins are rotated in the magnetic field, an AC voltage signal is generated to indicate speed of rotation. The two missing pins (set at 180° intervals) are a reference to TDC, and indicate crankshaft position by varying the signal as the flywheel spins. One missing pin indicates TDC for cylinders 1 and 4, and the other missing pin indicates TDC for cylinders 2 and 3. The peak-to-peak voltage of the speed signal can vary from 5 volts at idle to over 100 volts at 6000 rpm. The ECU contains an analogue-to-digital converter to transform the AC pulse into a digital signal.
The throttle potentiometer sensor (TPS) is provided to inform the ECU of rate of acceleration. The TPS is a potentiometer
with three wires. A 5.0 volt reference voltage is supplied to a resistance track, with the other end connected to earth. The third wire is
connected to an arm which wipes along the resistance track, and so varies the resistance and voltage of the signal returned to the ECU.
From the voltage returned, the ECU is able to calculate just how quickly the throttle is opened. From model year 1993 onwards, the
TPS also informs the ECU of idle position with a voltage of approximately 0.6 volts.
A fault will be indicated with the TPS circuit if the voltage reading is below 0.6 volts.
The air valve stepper motor is an actuator that the ECU uses to automatically control idle speed during normal idle and during engine warm-up. When the throttle is closed, the throttle valve is locked in a position where very little air passes by. The throttle position then, will have no effect upon the idle speed. A by-pass port to the throttle plate is located in the inlet manifold. A valve is positioned in the port. As the valve moves, the volume of air passing through the port will vary, and this directly affects the idle speed. The idle speed then, depends upon the position of the stepper air valve in the by-pass port. This method of idle control is fitted to some models (principally those with the plastic inlet manifold) from the middle of 1994.